Design Errors
Ensuring Quality Construction: Strategies to Avoid Design Defects
Introduction: In the realm of construction projects, success hinges on factors such as time, cost, and the ultimate quality of the finished product. Addressing design defects is crucial for achieving a flawless construction process. This article delves into Saudi Design Group’s construction defect checklist, categorizing design issues into three main types and exploring their causes and potential resolutions.Design Errors
I. Hardware Defects: 1.1 Unveiling Material Pitfalls: Material defects can significantly impact a project’s budget and timeline, arising from damaged building materials, whether originating from the manufacturer or developing on-site. Identifying these defects can be challenging, often surfacing only after incorporation into the project, leading to substantial costs.
II. Construction Defects: 2.1 Documenting Accuracy: Construction defects trace back to inaccuracies in the design team’s construction documentation. This may stem from negligence or errors, necessitating corrective measures like change orders or part replacements. Precision in design documentation is paramount for avoiding costly rework.
III. Manufacturing Defects: 3.1 Straying from Design Documents: Manufacturing defects occur when construction deviates from the meticulously laid out design documents. Ranging from cosmetic issues to compromised structural integrity, addressing manufacturing defects involves a complex process of assigning responsibility and rectification.Saudi Design Group
Common Causes of Design Errors:Design Errors-Design Errors
I. Inadequate Quality Control: 1.1 Skill Shortage and Material Quality: Insufficient quality control procedures often result from factors like a shortage of skilled workers, poor-quality materials, and unrealistic deadlines. Establishing robust inspection plans is essential for early defect identification, minimizing rework, and preserving project profitability.
II. Inefficient Document Distribution: 2.1 Overcoming Paper Circulation Challenges: Despite technological advancements, paper documents persist in circulating on construction sites and in back-office systems. Inefficient document management can lead to delays in signing and approving necessary documents, hindering project progress and potentially causing discrepancies in construction drawings.
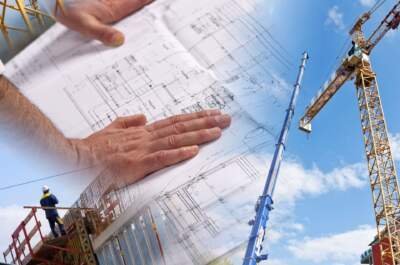
III. Poor Communication: 3.1 Mitigating Disagreements: Effective communication among project stakeholders, construction teams, employees, and contractors is vital for maintaining project momentum. Disagreements can impede progress and heighten the risk of construction defects, underscoring the importance of fostering collaborative communication channels.
Conclusion: Achieving a zero-defect construction project involves addressing hardware, construction, and manufacturing defects through proactive measures. By enhancing quality control, streamlining document distribution, and fostering clear communication, construction managers can minimize design errors and ensure the successful delivery of high-quality projects.